真空成形とは?特徴や強み、射出成形との違い、型・製品の材料など徹底解説
- 真空成形
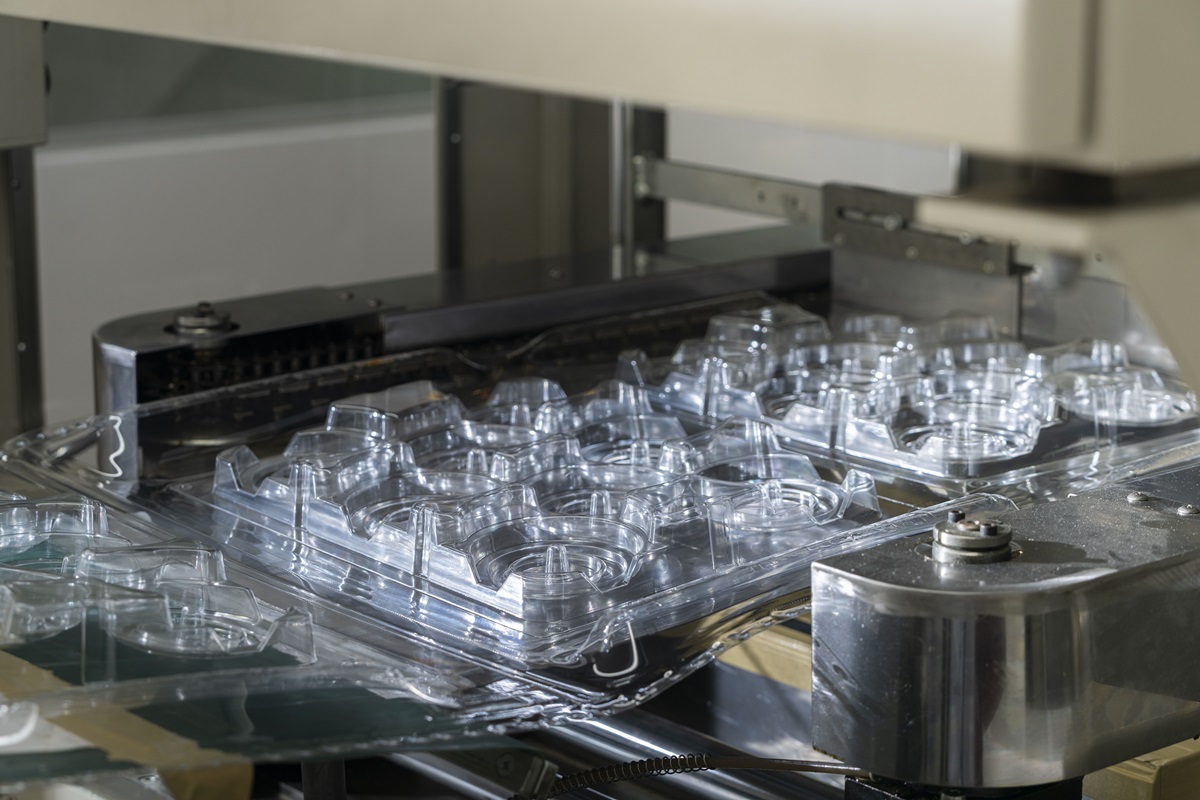
金型製作のコストが安く、多品種少量生産に向いている真空成形。
ローコストで様々なプラスチック製品を製造できますが、詳しく仕組みを理解されている方は、少ないでしょう。
そこで本記事にて、真空成形の特徴や他の成形方法との違いなどを徹底解説していきます。
具体的には、下記のような内容をまとめています。
- 真空成形の特徴と製造工程
- 真空成形のメリット・デメリット
- 真空成形で使われる樹脂や具体的な製品例
- 真空成形と射出成形、圧空成形、プレス成形の違い
今後、プラスチック製品の製造を検討されている方や試作品を作りたい方には、特に読んでいただきたい内容となっておりますので、ぜひご一読くださいね。
では真空成形の特徴から詳しくご紹介していきます。
TSK株式会社では、真空成形の設計から試作、開発までをサポートします。ぜひお気軽にご相談ください。
お問い合わせはこちら
真空成形とは
身の回りにある様々なプラスチック製品が、真空成形という製造方法で作られています。
具体的には、卵のケースやお弁当の容器、コロナ対策のアクリル板など、普段使っている物も真空成形で作られており、馴染みのある技術です。
これらの製品は、熱可塑性プラスチックという樹脂が材料。
代表的なものでは、下記のようなものがあります。
- ABS
- AES
- PMMA
- PC
- PP
- PE
- HIPS
- PET
- PVC
近年では、複合多層材料や印刷された材料が使用されることもあります。
(詳しくは、真空成形で使われる樹脂の項目で解説しておりますので、ご安心ください)
真空成形の仕組み
熱可塑性プラスチックは、熱を加えることで柔らかくなったり溶けたりし、冷やすと個体になるプラスチックです。
真空成形では、まず板状の熱可塑性プラスチックシート(以下「シート」という)に両面から熱を加えて柔らかくします。
次にそのシートを金型に合わせ成形していきますが、真空成形の金型には凸型と凹型があり、どちらか一方を使ってシートを成形します。
この金型には、小さな空気穴が空いており、そこからシートと金型の間の空気を吸引して、真空状態を作るのです。
真空状態になることで、シートが金型に密着し、シートに金型の形状が移ります。
最後に金型の形になったシートを冷やし固化させます。
すると、金型の形のままシートが固まり、成形の工程は完了です。
成形過程でどうしても出てしまう余分な部分をカットして、完成となります。
真空成形には5種類の成形方法がある
先程、真空成形の金型には、凸型と凹型があるとご紹介しました。
この凸型・凹型によって成形方法が異なり、凸型を使う場合はドレープ真空成形、凹型を使う場合はストレート真空成形と呼ばれます。
加えて、プラグアシスト真空成形・エアスリップ真空成形・真空圧空成形という成形方法もあります。
まとめると、下記の通りです。
- ストレート真空成形
- ドレープ真空成形
- プラグアシスト真空成形
- エアスリップ真空成形
- 真空圧空成形
それぞれの成形方法には、異なる特徴がありますので、1つずつ簡単にご紹介します。
ストレート真空成形
真空成形の中で最もスタンダードな成形方法であるストレート真空成形。
加熱して柔らかくしたシートを凹状の金型に張り付かせるような成形方法です。
凹状の金型とシートの間の空気を抜き真空状態にして、シートを金型の形状に成形します。
このストレート真空成形の主な特徴は、下記の通りです。
- 成形が簡単
- 成形品の外側が型に面することから外側の寸法の精度が高くなりやすい
- 同一シートで複数個の成形がしやすい
- 冷やす過程でシートが縮むため、型から外しやすい
- 比較的強度が強い
- 深絞りができず、厚みも底の角部分で薄くなりやすい
- 型にゴミや傷があると、成形品の外側にも現れてしまうため、外面を重視する場合は注意が必要
ドレープ真空成形
真空成形の基本的な成形方法の1つであるドレープ真空成形。
加熱して柔らかくしたシートを凸状の金型で突き上げ、シートを伸張した後に型とシートの間の空気を抜き成形します。
空気を抜く方法は、型とシートの間の空気を真空吸引する方法と、外側から圧縮した空気を入れて型とシートの間の空気を抜く方法の2種類があります。
このドレープ真空成形の主な特徴は、下記の通りです。
- ストレート真空成形同様、成形が簡単
- 成形品の内側が型に面することから、内側の寸法の精度が高くなりやすい
- ストレート真空成形よりも均一な肉厚の成形品ができる
- 比較的深絞りが可能
- 同じシートで複数個の成形品を作る場合は、分離格子を使用しなければならない
- 冷やす過程でシートが縮むため、型と成形品を剥がしにくくなる場合がある
- 型から剥がすために工夫が必要となる
- 横方向の強度が低下しやすい
- 側壁部分が薄くなりやすい
- 型にゴミや傷があると、成形品の内側にも現れてしまうため、内面を重視する場合は注意が必要
プラグアシスト真空成形
プラグアシスト真空成形とは、その名の通り、加熱し柔らかくなったシートをプラグと呼ばれる型で突き伸ばしながら(アシストしながら)真空成形する方法です。
金型は、凹状を用いるため、簡単に言うと、ストレート真空成形に補助を入れたような成形方法。
主な特徴は下記の通りです。
- 細かい部分まで精密に成形可能
- 同一シートで複数個の成形も可能
- 厚薄のムラが少ない
- 成形品の外側が型に面することから、外側の寸法の精度が高くなりやすい
- 冷やす過程でシートが縮むため、型から外しやすい
- プラグで突き伸ばすため、シートに大きな力を与えられる
エアスリップ真空成形(エアースリップ真空成形)
エアスリップ真空成形は、ドレープ真空成形に一手間加えた成形方法のようなものです。
具体的には、まず加熱し柔らかくなったシートを圧縮した空気で膨らませます。
次にそのシートへ凸状の型を突き上げます。
最後に、真空吸引することでシートを型に密着させ成形します。
主な特徴は下記の通りです。
- 表面の仕上がりが滑らかになりやすい
- ドレープ真空成形よりも深い成形ができる
- 厚薄のムラが少ない
- 強度が出やすい
真空圧空成形
真空圧空成形は、真空吸引していない側のシートに圧縮した空気を送り込み、型にシートを押し付ける力もプラスした成形方法です。
真空にした状態の力では、大気圧以上の力をシートにかけられませんが、真空圧空成形では圧縮した空気の押し付ける力も加えられるため、より強い力でシートを成形することができます。
それにより細部まで精密な成形が可能。
一方で、他の真空成形の成形方法に比べて型にも大きな負荷がかかることから、他の成形方法よりも型の強度を上げなければならないというデメリットもあります。
ここまで真空成形の成形方法について5つご紹介してきました。
次では、真空成形の製造工程についてスポットを当ててみたいと思います。
真空成形の製造工程には2種類ある
真空成形の製造工程には、単発真空成形と連続真空成形の2種類があります。
ではそれぞれの特徴と工程を詳しくみていきましょう。
単発真空成形の特徴と工程
単発真空成形に用いられる機械は、単発真空成形機と呼ばれます。
この機械では、単板状の枚葉(まいよう)シートと呼ばれる熱可塑性プラスチックシートを材料にします。
製造工程は、その名の通り1枚1枚加工していく成形方法で、単板状の枚葉シートに熱を加えて柔らかくし、シートと金型との間を真空状態にして、型にシートを密着させて成形する方法です。
単発真空成形の主な特徴は次の3つです。
- 多品種少量生産に向いている
- 成形品の表面が型に当たらないため、柔らかなラインを作りやすい
- 複合多層材料や印刷シート、加飾シートを使うことで、様々な表面状態・加飾が表現可能
自動車の内容やPC、アミューズメント機器などの製品を成形する際によく用いられる成形方法になります。
連続真空成形の特徴と工程
連続真空成形で用いられる機械は、連続成形機と呼ばれます。
連続とある通り、シートを連続で金型へ供給し、ライン作業のように熱を加えて成形、冷却、型から外す、という一連の工程で真空成形ができます。(このシートは、ロール状であることもあります)
連続真空成形の特徴は、連続で成形できることから、大量生産が可能な点です。
一方で、肉厚の薄い成形品が主な加工品となります。
具体的には、お弁当のプラスチック容器やトレー、ブリスターパックなどです。
真空成形の6つのメリット
ここからは真空成形の主なメリットを下記の6つご紹介していきます。
- 生産コストが安価
- 生産までが比較的スピーディー
- 凹凸のどちらでも成形可能
- 試作から量産まで柔軟に対応できる
- 複合多層材料や様々なシートに対応でき、材料の自由度が高い
- 材料の厚みや成形品の大きさも比較的自由度が高い
では1つずつ詳しくチェックしていきましょう。
生産コストが安価
真空成形の型は、射出成形に比べて安価に製造できます。
具体的には、射出成形の5分の1から10分の1程度の費用で済んでしまいます。
真空成形が射出成形に比べ、これほどまでに安価に製造できる理由としては、2つあります。
1つ目は、真空成形では凹凸どちらかの型のみで成形できる点です。
2つ目は、真空成形はシートと型の間を真空にし、大気圧を利用して成形することから、成形圧力が弱いという特徴があり、型に強度がそこまで必要ない点です。
金型の材料には、金属以外を使用することもでき、試作段階では木製や樹脂製の型を使うこともあります。
そのため、型の製造コストを抑えられることで、他の成形方法よりも生産コストを安くすることができます。
生産までが比較的スピーディー
木製や樹脂製の型を使うことができるため、型の加工が比較的容易に行えます。
そのため、試作から生産までをスピーディーに行うことが可能です。
成形品にもよりますが、おおよそ1ヶ月程度で金型を製作でき、生産体制に移行できるでしょう。
凹凸のどちらでも成形可能
真空成形では、凹凸のどちらでも成形が可能です。
上手く成形できれば、成形品の表面処理をなくすこともできます。
試作から量産まで柔軟に対応できる
木製や樹脂製でも型を作成できるため、低コストで試作を行えますし、デザインの変更も射出成形に比べて容易に行えます。
そのため、少ないロット数での生産が可能で、気軽に試作品を作れます。
加えて、試作で製造した型を基に金型を作れますので、量産も可能です。
真空成形は、型の製造コストも低いことから、多品種少量生産に向いています。
複合多層材料や様々なシートに対応でき、材料の自由度が高い
真空成形で加えられる力は、大気圧程度であり、凹凸どちらかの型を用いるため、様々なシートを成形できます。
具体的には、硬質や軟質、発泡シート、不織物などの異なる材料を複合させた物や印刷シートや加飾シート、機能性シートなどです。
材料の厚みや成形品の大きさも比較的自由度が高い
真空成形で用いる材料の厚みは、0.15mmから1cm程度まで対応でき、比較的自由度が高いです。
また、比較的大きなサイズの成形品にも対応できます。
真空成形の4つのデメリット
生産コストが安価で、試作から量産までスピーディーに対応できる真空成形ですが、デメリットも存在します。
そこでここからは真空成形のデメリットを4つご紹介していきます。
これから試作品を作ろうとしている方や真空成形を取り入れようとしている方は、ぜひチェックしてみてください。
ボスを付けられない
ボスとは、成形品を組み合わせる際や他の部品と締結する際に使用される結合部分のことです。
凸状のネジ穴やピンをはめる穴として使われれます。
真空成形では、このボスを成形過程で取り付けることができません。
必ず、成形後のシートに接着剤や加工などで取り付けることになります。
不要な部分のカットが必要になる
真空成形する際、シートを固定したり型とシートの間を真空にしたりするための部分が必要になります。
つまり製品とは関係ない部分が少なからず成形品には含まれてしまうため、真空成形した後に不要な部分をカット(トリミング)しなければなりません。
厚みや寸法にバラツキが出やすい
真空成形では、シートを型に当てて引き伸ばすため、どうしても部分的に肉厚が薄くなったり、型に当たらない箇所の寸法がズレたりしてしまいます。
プラグアシスト真空成形やエアスリップ真空成形、真空圧空成形などの成形方法にすることで、このデメリットを緩和することは可能です。
(単発真空成形の場合)サイクルタイムが長くなりやすい・製品代が高くなりやすい
単発真空成形の場合は、連続真空成形や射出成形と比べて、1つの製品を成形するまでにかかる時間が長くなりやすいというデメリットがあります。
さらに、射出成形に比べて単発真空成形の場合、製品のコストが高くなりやすいというデメリットもありますので、注意が必要です。
真空成形で使われる樹脂(熱可塑性プラスチックシート)
真空成形では、様々な材料を成形することが可能です。
代表的な材料は、ABS・AES・PP・PE・PCなどが挙げられます。
さらに硬質や軟質、発泡シート、不織物などの異なる材料を複合させた複合多層材料や印刷シートや加飾シート、機能性シートなども成形可能です。
その他も材料も含めて、ここで簡単に特徴をご紹介しておきます。
成形可能な主な材料一覧 | |
材料 | 特徴 |
ABS樹脂 | A=アクリロニトリル・B=ブタジエン・S=スチレンの3種類の成分を組み合わせた樹脂のことです。それぞれの性質を得ており、取り扱いやすい材料です。着色することができ、光沢もあります。また強度のバランスにも優れています。そのため、デザイン性や外観を重視する物に使用されるプラスチックです。 |
AES樹脂 | ABS樹脂と同じような性質がありますが、B=ブタジエンではなく、E=エチレンを使用しているため、耐候性があり、屋外で使用される物に向いている材料です。 |
PP樹脂 | PP樹脂(ポリプロピレン)は、炭素と水素のみの重合体です。耐熱性や機械強度に優れており、軽く傷つきにくい材料です。安価に大量生産しやすいメリットもあります。 |
PE樹脂 | PE樹脂(ポリエチレン)は、原料価格が安く、加工しやすいため、大量に生産する製品の材料に向いています。また、身の回りの様々な物に使われている材料です。 |
PC樹脂 | PC樹脂(ポリカーボネート)は、ガラスのような透明性を持ち、衝撃にも強いプラスチック。紫外線に強い特性があることから、屋外で使用できるという特徴もあります。また自己消火性を持っています。 |
PMMA樹脂 | PMMA樹脂(アクリル)は、PCの透明性よりも優れており、その透明度はガラスを超えます。さらに高い耐候性と強度を持ちながら軽量であり、加工もしやすい材料です。 |
PMMA-ABS | ABS樹脂の板とアクシル板を重ねた材料です。光の輝きが非常に強く、アミューズメント製品など華やかな成形品の材料に使われます。 |
PMMA-AES-ABS | 上記の材料にAES樹脂の板を加えた3層の材料です。AES樹脂を加えることで、耐候性がプラスされます。 |
メッキ調ABS | ABS樹脂の板にメッキ調のフィルムを加えた材料です。メッキの製品に比べて、環境負荷が少ない反面、輝度は劣ります。また、ABS樹脂に比べて加工性も劣ってしまいます。 |
PS樹脂 | PS樹脂(ポリスチレン)は、ガラスに近い透明性を持ち、軽量かつ加工しやすい材料です。透明性・耐候性ではアクリルに劣ります。 |
カイダック | カイダック(塩化ビニル樹脂プレート)は、高い耐衝撃性・耐薬品性を持ち、難燃性にも優れる材料です。 |
ロア | PC(ポリカーボネート)/ABS系の材料です。高い耐衝撃性・耐熱性を持ち、難燃性にも優れる材料で、カイダックの代替品として開発されました。 |
PW樹脂 | PP樹脂とPE樹脂を混ぜ、PP樹脂よりも成形しやすい材料です。耐衝撃性に優れる特徴があります。 |
PET樹脂 | PET樹脂(ポリエチレンテレフタレート)は、ペットボトルの原料でお馴染みの樹脂です。耐衝撃性と透明性、食品衛生性に優れている材料です。 |
PVC樹脂 | PVC樹脂(塩化ビニル樹脂)は、塩化ビニルの重合体の材料で、高い耐水性と耐薬品性、難燃性を持ち合わせています。また電気絶縁性にも優れている特徴があります。 |
変性PPO(m-PPE) | 変性PPO(変性ポリフェニレンエーテル)は、成形性を高めるため、ポリスチレン系樹脂と混ぜ、変性した材料です。耐熱性と耐衝撃性に優れます。 |
タフビロン | タフビロンは、アクリル変性高衝撃プレートで、難燃性・耐衝撃性・耐薬品性に優れた材料です。 |
真空成形の型を作る材料と各材料の特徴
真空成形の型を作る材料は、主に木や樹脂、アルミなどの金属です。
試作段階では、木製や樹脂製で型を作り、量産段階では樹脂性や金属製で型を作るのが一般的です。
それぞれの材料により特徴(型の材料費や加工費、製作日数など)が異なりますので、型の材料を選ぶ際は、成形品の形状や精度、かけられる予算などを総合的に検討して選択します。
ではそれぞれの特徴を細かくみていきましょう。
木製の型の特徴
木製の型の特徴は、材料費や加工費が安価かつ短期間で型を作ることができる点です。
一方で木の表面をツルツルにするのが難しいため、成形品の表面状態を綺麗にするのが難しかったり、成形品に木目が写ってしまったりする弱点があります。
また、型の作りによっては、成形品にヒビ割れができてしまうこともあるでしょう。
木は熱伝導率が悪いため、成形品の冷却に時間がかかってしまう点もデメリットです。
耐久性はなく、使用回数は数回に限られてしまいます。
樹脂製の型の特徴
木製の型と同じく短期間で型を作ることが可能です。
試作段階で作った木製の型を原型(マスター型)に使用できるというメリットもあります。
一方で木製同様、熱伝導率が悪く成形品の冷却に時間がかかってしまうというのがデメリットです。
型の温度調節ができないため、成形品にソリが発生してしまうこともありますし、鋭い形状の成形にも向きませんが、成形品の量産ができます。
数万回の使用にも耐えるように型を製作することも可能です。
金属製の型(金型)の特徴
上記の素材に比べ、加工に手間がかかり、素材も高価なことから木製の型・樹脂製の型に比べて、型の製作コストがかかってしまいます。
しかし、優れた強度と耐久性、綺麗な表面の型になるため、質の高い成形品を量産することができます。
さらに高い熱伝導率を利用して、型の温度を調整できるため、ソリの少ない精度の高い成形を可能にします。
真空成形で作れる製品の具体例
真空成形では、身の回りにある様々なプラスチック製品を成形することが可能です。
では具体的にどのような製品が真空成形によって作られているのか、主な製品をご紹介していきます。
日用品や生活用品など手に取る機会のある製品では、卵のケースやお弁当のプレート、ゲーム機やパソコンのカバーなどです。
その他の製品は、下記のような物に真空成形が用いられています。
- 自動販売機のドリンクサンプルやパネル
- 浴槽や洗面台、照明カバー、洗濯機の防水パン
- 自動車のメーター類やインパネ部分などの内装品、バンパーやヘッドライトなどの外装品
- 航空機や電車、重機、農機などの樹脂カバー
- 配送トレーやパレット、看板、商品棚などの業務用品
- 医療機器やリハビリ機器のカバー
- フィギィアやアミューズメント機器
これは真空成形で作られている製品のほんの一部に過ぎません。
真空成形は、多種多様なプラスチック製品の製造を可能にしています。
真空成形と射出成形、圧空成形、プレス成形の違い
プラスチック製品の成形方法は、真空成形だけでなく、射出成形や圧空成形、プレス成形などもありますが、各製法の特徴や違いまで詳細に把握している方は少ないでしょう。
製造したい製品の成形にどの製法が適しているか判断するためにも、そこでそれぞれの違いについてまとめていきます。
成形方法 | 真空成形 | 射出成形 | 圧空成形 | プレス成形 |
型の材料 | 木製や樹脂製、金属製 | 金属製 | 木製や樹脂製、金属製 | 金属製 |
型の製造コスト | 安価 | 高価 | 安価(真空成形の型よりは高い) | 高価 |
型の製造にかかる期間 | 2週間程度 | 1ヶ月程度 | 2週間程度 | 1ヶ月程度 |
製品代 | 単発真空成形では高価 | 真空成形・圧空成形に比べると高価 | 単発の成形では高価 | 真空成形・圧空成形に比べると高価 |
試作 | 容易 | 難しい | 容易 | 難しい |
型の調整 | 比較的容易にできる | 難しい | 比較的容易にできる | 可能 |
色の変更 | ロットごとに対応できる | ロットごとに対応できるが、大ロットでの成形となるため、細かく変更できるとはいえない | ロットごとに対応できる | 可能 |
成形品の形状 | 成形方法によって深絞り成形が可能 | 形状の制限が少ない | 射出成形と同じレベルのシャープな成形が可能 | 形状には制限がある |
外観 | 成形方法によっては射出成形と同レベル | 非常に良い | 非常に良い | 非常に良い |
ロット | 小ロットから中ロット | 大ロット | 小ロットから中ロット | 大ロットが基本 |
成形品の大きさ | 同じ機械で小さい物から大型の物まで成形可能 | 機械によって制限がある | 同じ機械で小さい物から大型の物まで成形可能 | 機械によって制限がある |
特徴 | 成形する力が弱いため、木製や樹脂製でも型を作れ、安価に製品を製造可能。 そのため多品種少量生産から大量生産まで適応できる |
真空成形では成形できないような複雑な成形が可能。 さらに連続した成形もできるため、大量生産に向いている |
真空成形よりも強い力を加えられるため、射出成形と同レベルの表面形状を成形できる | 透明品や看板などの製品の成形に向いている 真空成形・圧空成形で成形できない伸びにくい材料の成形も可能 |
【Q&A】真空成形に関する疑問・気になるポイント
ここでは、真空成形に関する疑問や気になるポイントなどを一挙にまとめてみました。
- 何個から成形可能ですか?
- 真空成形のメリットは何ですか?
- 透明な材料はありますか?
- 透明やスモークなどの製品は成形可能ですか?
- 真空成形の金型は射出成形の金型より安価ですか?
- 真空成形の型の材料は金属のみですか?
- 素材の厚みは何mmほどですか?
- 真空成形した製品の厚みは均一になりますか?
- 真空成形で寸法の安定性が高い材質は何ですか?
- 製品の表面にネジ穴を開けたくない場合はどうすれば良いですか?
- 耐熱性の高い材料を使いたいのですが、ありますか?
- 屋外で使用できるようにするにはどうすれば良いですか?
- 真空成形機のメーカーは、日本に何社ありますか?
製品の試作や量産を検討している方など、ぜひ参考にしてみてくださいね。
何個から成形可能ですか?
1個から成形することができます。
ただ型を作る必要がありますので、初期費用はかかってしまいますが、射出成形よりコストを抑えられます。
真空成形のメリットは何ですか?
真空成形のメリットは、射出成形よりも型の製作や試作などを安くできる点です。
また型の製作も短期間で行うことができ、試作から大量生産、また成形品の大きさまで柔軟に対応できます。
透明な材料はありますか?
PC樹脂(ポリカーボネート樹脂)やPMMA樹脂(アクリル樹脂)、PET樹脂など、透明な材料があります。
透明やスモークなどの製品は成形可能ですか?
PMMA樹脂(アクリル樹脂)などの透明な材料を使うことで、透明にすることができます。
またスモークも可能です。
真空成形の金型は射出成形の金型より安価ですか?
真空成形の金型は、凹凸のどちらかの型のみで成形可能なため、射出成形よりも安価に型を作ることができます。
真空成形の型の材料は金属のみですか?
試作段階では、木製や樹脂製で型を作ることが可能です。
また、生産段階では樹脂製で型を作ることもあります。
素材の厚みは何mmほどですか?
一般的に0.15mmから1cm程度まで対応できます。
真空成形した製品の厚みは均一になりますか?
材料のシートを突き上げたり、引き伸ばしたりするため、製品の厚みは均一になりません。
真空成形で寸法の安定性が高い材質は何ですか?
ABS樹脂が寸法安定性の高い材料になります。
製品の表面にネジ穴を開けたくない場合はどうすれば良いですか?
成形後に裏面にボスを接着したり、裏部品を製作し接着したりする方法があります。
耐熱性の高い材料を使いたいのですが、ありますか?
PC樹脂(ポリカーボネート樹脂)やPMMA樹脂(アクリル樹脂)などが耐熱性に優れた材料になります。
屋外で使用できるようにするにはどうすれば良いですか?
耐候性に優れる材料を使うことで、屋外でも使用できるようになります。
材料は、PMMA-AES-ABSやPMMA樹脂(アクリル樹脂)、PC樹脂などが該当します。
真空成形機のメーカーは、日本に何社ありますか?
20社以上のメーカーがあります。
まとめ|試作から生産・物流まで対応のTSK株式会社までご相談を
ここまで真空成形の特徴やメリット・デメリットなどをご紹介してきました。
射出成形に比べて安価に型を製造でき、試作から大量生産まで柔軟に対応できる真空成形は、多品種少量生産に向いています。
厚みや寸法にバラツキが出やすいなどのデメリットもありますが、ローコストかつスピーディーに設計から生産へ移行できるため、これから製品を作ろうとしている方は、ぜひ検討しておきたい成形方法です。
TSK株式会社では、真空成形の設計から試作、開発までをサポートしますので、ぜひお気軽にご相談ください。