technology 解決できる課題
トレイの材質変更で工程を削減
部品の製造ラインでこんなお悩みを抱えていませんか?
- 完成部品を仮置き容器から出荷用トレイに移し替える作業工数を削減したい。
- コネクタなど、樹脂を溶かして注入する工程のある部品の冷却を待たずにプラスチックトレイにセットしたい。
完成部品の保管容器と出荷用トレイを1つのトレイに統一
Before 製造直後のハーネスを冷ますための仮置き作業が発生
ハーネスの製造工程では樹脂部分が110℃~120℃前後の高温になっているため、ハーネスが冷却できるまでは仮置き容器に保管していました。出荷の際はPP製の真空成形トレイを使用していましたが、部品完成直後の高温状態では溶けてしまうため、部品の冷却後に出荷用トレイに移し替えていました。
部品を移し替える作業工程をどうにか改善できないかという長年の悩みを抱えていました。
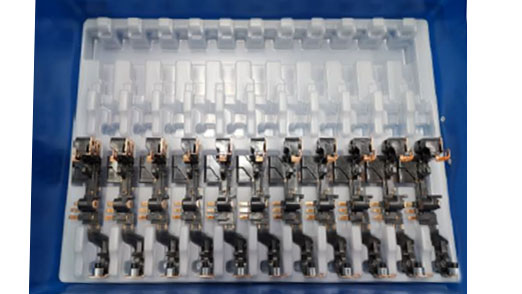
After
135℃の耐熱温度がある耐熱PPシートを使用した真空成形トレイを提案しました。変更後は、部品が仕上がった段階で出荷用トレイにセットできるようになりました。部品を仮置き容器に入れて冷ます工程と、仮置き容器から出荷用トレイに移し替える工程が削減できました。
コネクターなどの樹脂を溶かして注入する必要のある部品において、上記のような問題を抱えている製造ラインは多いのではないでしょうか?出荷用トレイに耐熱PPの真空成形トレイを活用することで出荷作業の改善が期待できます。
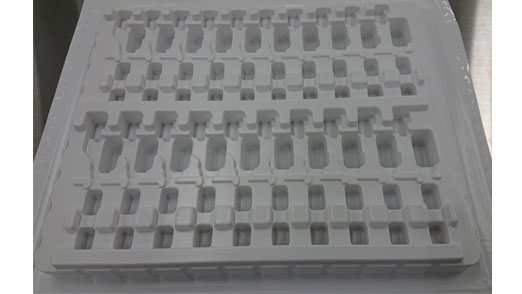
今回の事例のポイント
1.特徴が異なる真空成形トレイの材質の中で、製造工程を考慮した材質での提案で作業効率改善をお手伝いします。
2.自動車部品の輸送でトレイに付着した油の高温洗浄など、高温洗浄作業が必要な通いトレイにも活用できる事例となります。
3.包装トランスフォーメーションを行うことで作業効率やコストダウンといったお客様のニーズを実現します。