technology 解決できる課題
包装材選びで物流課題を解決!電動車部品メーカーの真空成形活用事例①
- 包装設計
- 調達担当者
- 電動車用部品
電動車の開発競争が激化する中、自動車部品メーカーはタイトなスケジュール内で迅速かつ効率的に包装仕様を決定しなければなりません。
しかし、開発担当者の知識不足や包装材の選択ミスにより出荷作業が複雑化し、コストや作業負担の改善ができずに悩む企業が少なくありません。
今回、電動車用部品メーカーが直面する物流包装の課題と、それを解決する真空成形の活用事例をご紹介します。
自社内での包装材選びの難解さ
ある電動車用部品メーカーでは既製品の包装材を組み合わせて使用していましたが、多重包装により作業効率が悪化。また、社内で包装設計の専門知識もつ担当者がいないため、選んだ包装材が輸送中の部品を十分に保護できるか不安が残る状況でした。
お客様の実際の声
- 多重包装による手間の増加:既製品の緩衝材を重ねて使用することで、包装作業に時間がかかる。
- 専門知識の不足:真空成形トレイを選んでも、部品が傷つかず輸送できるか確証が持てない。
真空成形も選択肢のひとつ
包装材選定の際に、よく聞かれるお客様のニーズを挙げてみます。
- 積載効率の向上:空間設計により輸送効率を最大化したい。
- コスト削減:型や輸送費など全体で見たときにコストを下げたい。
- 作業時間の短縮:人手不足で、出荷作業の作業を簡易化したい。
TSKは包装材の設計製造メーカーの経験を生かして真空成形の設計・製造の事業を立ち上げました。真空成形だけでは部品の輸送包装は完結しませんが、多様な包装材の知識を総動員して積載効率を向上させる空間設計や、製品特性に応じた最適な包装材の選定を行います。
真空成形+α! 複数の材質で比較提案いたします
包装設計の手間いらずで簡単に導入できる緩衝材として、エアー緩衝材や気泡緩衝材があります。簡単に入手でき、カットしたりそのまま包むだけで導入できるので使用されているメーカーも多いのではないでしょうか。
しかし、どこまで緩衝材を使用すれば中に入れた部品を壊さずにユーザーのもとに届けられるのか判断できず、何重にも重ねて包装しているのはコストや作業工数のロスにつながります。
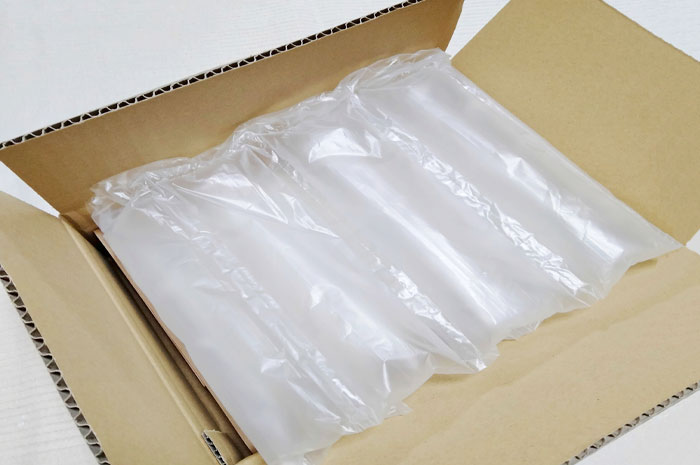
TSKでは真空成形以外の包装材も活用し、部品輸送に最適な輸送形態を提案しています。
真空成形トレイ・発泡緩衝材・規格トレイのパターン別で提案した実例です。
自動車部品メーカー様での資材コストの比較例
【月間1,000箱として比較 単位:円】
メイン資材 | エアー緩衝材(現行) | 発泡緩衝材 | 真空成形緩衝材 |
---|---|---|---|
外箱 | 100 | 100 | 100 |
個装袋 | 5 | 5 | 5 |
気泡緩衝材 | - | - | 5 |
緩衝材パッド | 250 | 300 | 150 |
合計(箱) | 355 | 405 | 260 |
コストダウン (年間) |
- | +600,000 | ▲1,140,000 |
コスト・作業時間・保管スペースをトータルで比較
資材コストでは真空成形にメリットがあり、包装作業時間では発泡緩衝材にメリットがでました。資材発注から出荷までをトータルで考えてみると、どの緩衝材にメリットが出てくるでしょうか?
メイン資材 | エアー緩衝材(現行) | 発泡緩衝材 | 真空成形緩衝材 |
---|---|---|---|
資材コスト | ○ | △ | ◎ |
包装作業時間 | × | ◎ | ○ |
保管スペース | △ | × | ◎ |
トータル メリット |
○ | △ | ◎ |
コスト面だけでなく、包装作業時間や保管スペースも合わせて比較した結果、真空成形がトータルで最も大きなメリットがでることがわかりました。
導入のポイント
今回のケースでは、真空成形の導入が課題解決に繋がりコスト削減と作業効率の向上を実現しました。また、複数の包装材の選択肢と設計知識を持つメーカーと連携することで、包装に関する不安を解消できました。
物流課題の解決には単なる包装材の選定に留まらず、全体の効率化をトータルで考えることが重要です。真空成形をはじめとする専門技術を活用して物流の最適化を模索してみませんか?