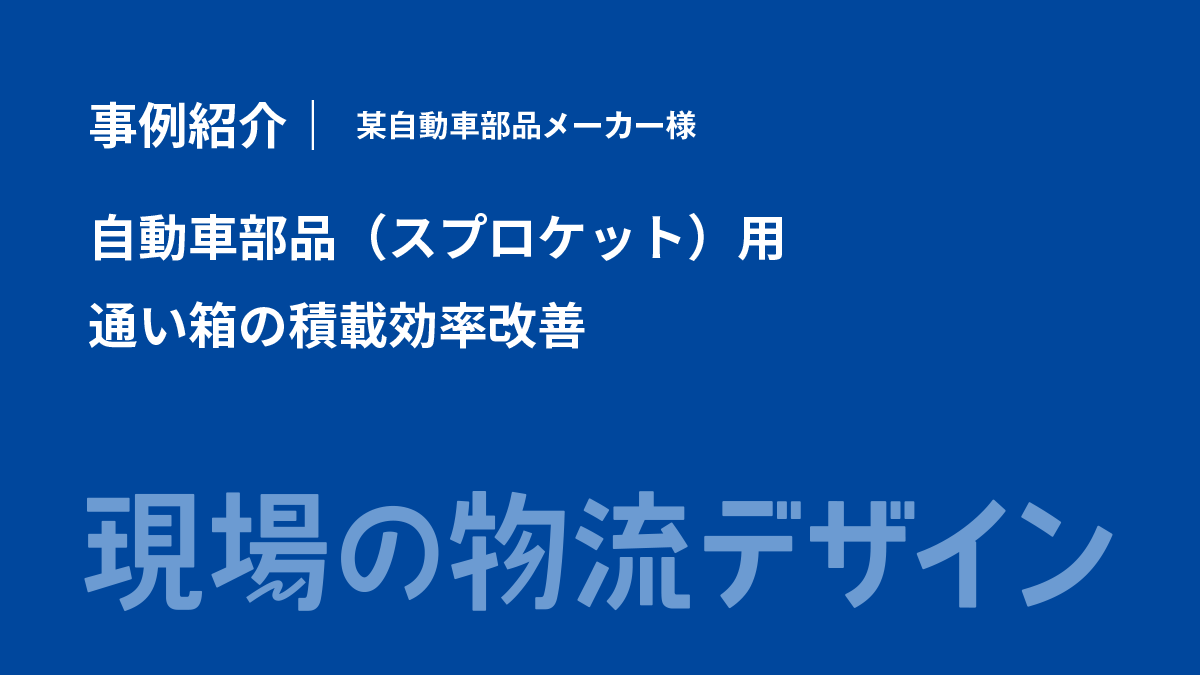
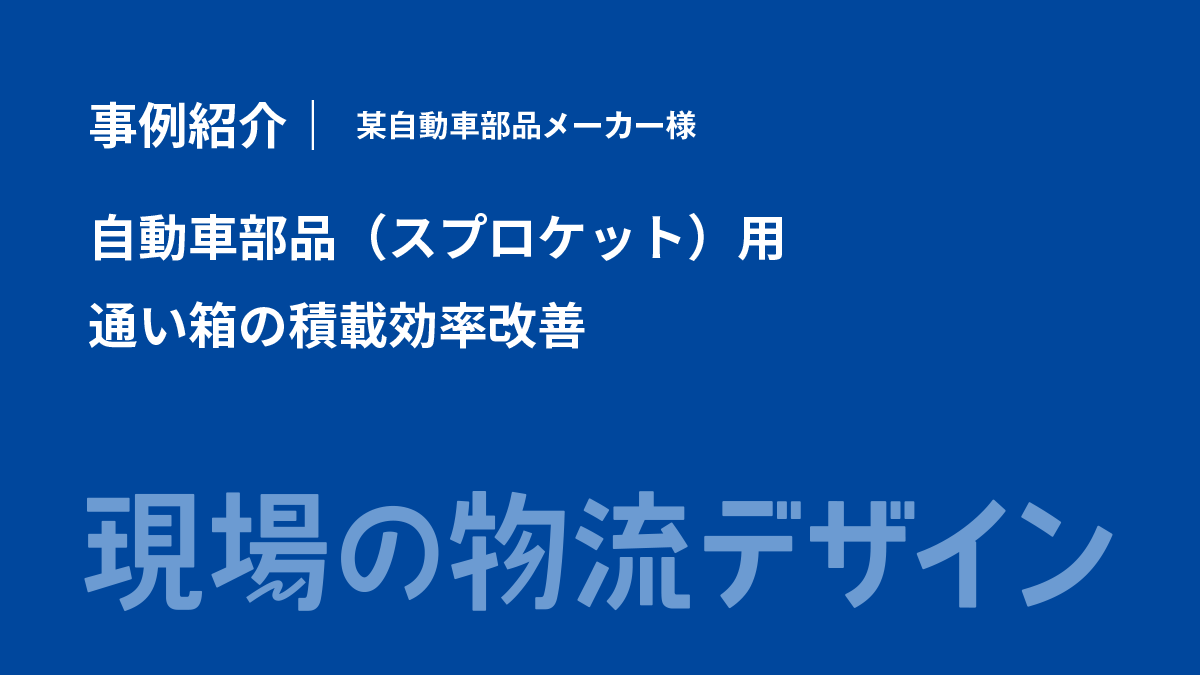
【事例紹介】自動車部品(スプロケット)用 通い箱の積載効率改善(自動車部品メーカー様)
TSKは“現場の物流をデザインする会社”として、輸送包装の領域で安全にモノを運ぶための緩衝設計や、最適なコストでモノを運ぶための空間・構造設計を行っています。この記事では、TSKがこれまでに手がけた包装設計の実事例をご紹介します。
今回取り上げるのは、某自動車部品メーカー様の「自動車部品(スプロケット)用 通い箱の積載効率改善」です。この事例では、プラスチックコンテナへの製品収納個数を増やし、積載効率の向上を実現しました。
一箱あたりの収納個数を6個→8個に
本事例では、自動車部品(スプロケット)の洗浄・出荷時に使用する包装材の改善を行いました。従来、プラスチックコンテナ一箱あたりの収納個数は6個でしたが、改善後は8個まで収納可能となりました。
▲収納方式を縦置きから横置きに変更。コンテナ内の空間を最大限活用することで、一箱あたりの収納個数を2個分増やすことができました。
積載効率25%アップ
横置きへの変更に伴い、仕切材の枚数を増やし、素材を低倍発泡性PPシートに変更して強度を高めました。この仕様変更により包装資材の費用は従来の倍となりましたが、一箱あたりの収納個数を増やしたことで、1枚のパレットに積載できる製品の総個数は216個増加、積載効率が25%向上しました。
この結果、包装資材費の増加分を上回る、年間で312万円の輸送コストの削減効果が得られました。
洗浄用と出荷用の包装を兼用化
さらにこの改善では、それまで別々に用意していた洗浄用と出荷用の包装材の兼用化を行いました。約70~80度の洗浄水に耐えられる素材を使用し、仕切材に穴や切り欠きを設けて洗浄後の水はけを良くすることで、出荷用の包装材をそのまま洗浄工程でも使用できるよう工夫。
これにより、洗浄後に出荷用の包装材に詰め替える作業をなくし、兼用化によって包装材コストの削減にも成功しました。
まとめ
近年の物流コストの内訳は、輸送費が半分以上を占め、保管費、包装費…と続きます。
今回の改善では、包装材費が倍増しても一箱当たりの収納個数を増やし、輸送費を削減することで、物流コストを大幅に削減することができました。また、燃料費削減によるCO2排出量の低減は、地球環境への負担を減らすことにもつながり、サステナビリティの観点からも意義のある取り組みとなりました。
さらに、包装材の材質を見直し、洗浄用と出荷用の包装材を兼用化することで、工場内物流における前後工程のシームレスな接続も可能にしました。
このようにTSKでは、製品の包装の仕方だけでなく運び方全体をデザインし、安全で効率的な物流の実現に貢献しています。現場の物流にお悩みがある方は、ぜひお気軽にお問い合わせください。